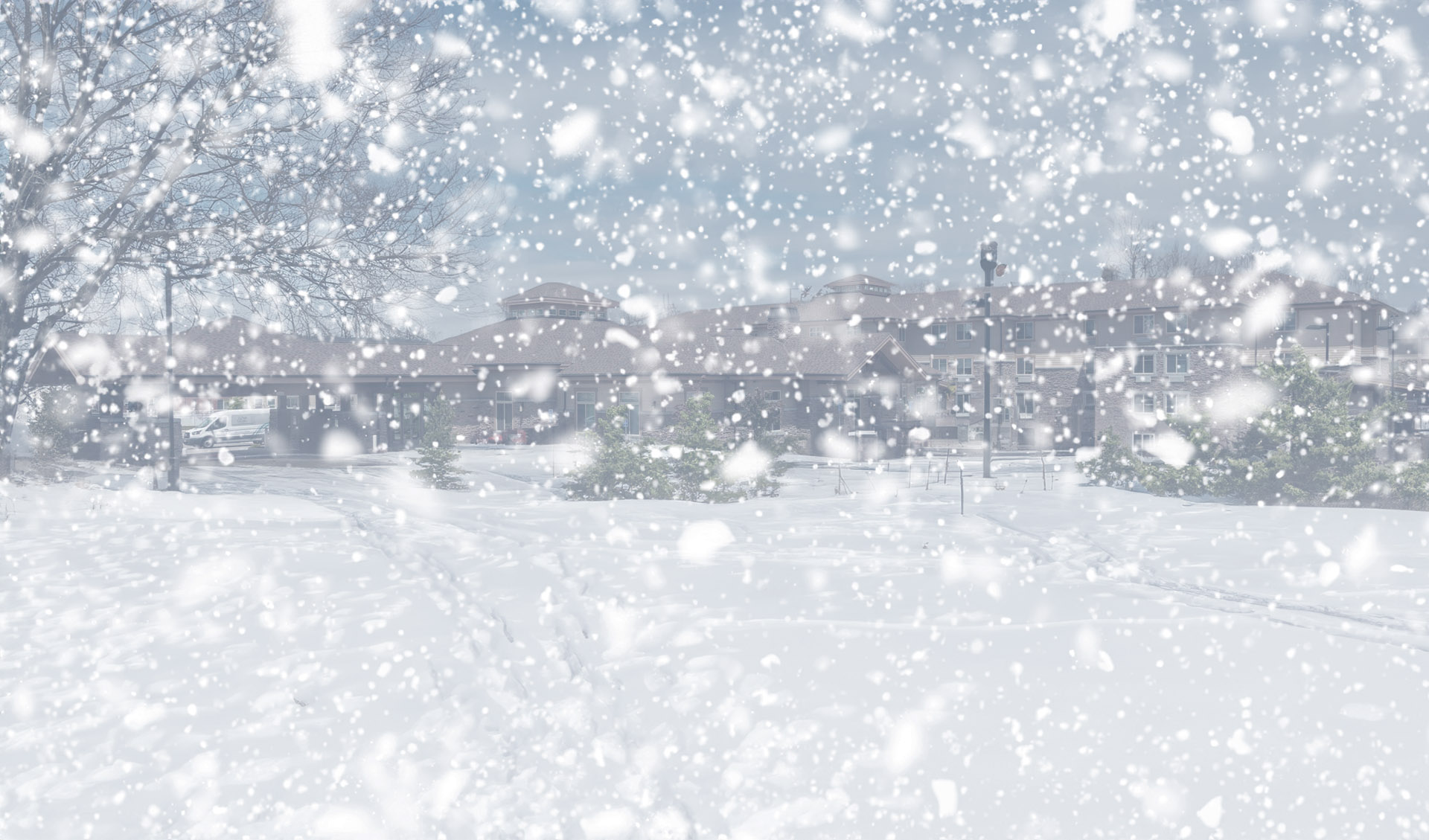
Snowmelt System Design Considerations
Introduction
When your architectural team designs a project in a climate where snow is possible, it is important to determine the type of snowmelt system needed and establish proper expectations of how the system chosen will perform. It will be necessary to find out the level of protection desired, the energy source, the snowmelt area surface type and then have the design team consider the general requirements of the snowmelt system. A qualified MEP engineering firm like Royal Engineering can help with this. Consider these:
- Level of Protection: Discussing the Snowmelt Classifications with the client will aid in determining the level of protection that is desired. Note that decisions regarding the Snowmelt Classifications (describe the amount of snow on the snowmelt area surface) will affect the cost of installation and the operating cost.
-
- Class I (0.0 free area) – The system will allow full accumulation before melting the snow. The client will tolerate complete coverage of snow on the surface. The surface will then clear after several hours of system operation.
- Used for low-risk residential areas (residential).
- This will be the lowest cost system to install and operate.
- Class I (0.0 free area) – The system will allow full accumulation before melting the snow. The client will tolerate complete coverage of snow on the surface. The surface will then clear after several hours of system operation.
-
- Class II (0.5 free area) – The system will allow half accumulation before melting the snow (essentially slush), with 50% of the snow melting on contact.
- Used for moderate risk commercial projects (residential, light commercial).
- Length of time that the slush will remain depends on rate of snowfall, wind speed, amount of water in the snow and the rate that water drains off of the snowmelt area.
- This will have a system cost and operating cost that is more than Class I and less than Class III systems.
- Class II (0.5 free area) – The system will allow half accumulation before melting the snow (essentially slush), with 50% of the snow melting on contact.
-
- Class III (1.0 free area) – The system will try to keep up with the rate of snowfall, provides completely snow-free area even during a storm. This provides 100% of the snow melting on contact 99% of the time that snowfall occurs.
- Any snow accumulation should be melted very quickly.
- Used for high-risk institutional areas (hospital ER entrance, heliport landing pad, loading docks).
- Critical areas will have more piping with less distance between the pipes.
- This will be the highest cost system to install and operate.
- It is likely that most clients mistakenly expect all snowmelt systems to operate in this manner.
- Class III (1.0 free area) – The system will try to keep up with the rate of snowfall, provides completely snow-free area even during a storm. This provides 100% of the snow melting on contact 99% of the time that snowfall occurs.
- Energy Source: Traditional Snowmelt Systems use Gas Fired Boilers. Smaller Snowmelt Areas often use Electric Mats. It is becoming more popular to have all-electric buildings that would need to use an Electric Boiler.
- Gas Fired Boiler
- Most often Natural Gas or Propane.
- System will be comprised of a boiler, system controls, manifolds and piping system filled with glycol.
- Will require maintenance personnel (similar to building hydronic system).
- Will require a gas connection (in municipalities that permit the use of gas heating).
- This system will cost more than an Electric Mat system.
- Gas Fired Boiler
-
- Electric Mats
- Can be installed using preassembled mats of wire or using hand-installed coils of electrical heating wire.
- Most often used for snowmelt areas of 1,500 square feet or smaller.
- System will be comprised of heating wire and system controls.
- This system will not require maintenance.
- This system will cost less than the hydronic systems with glycol filled piping networks.
- Electric Mats
-
- Electric Boiler
- Electric only and will not have a gas connection.
- System will be comprised of a boiler, system controls, manifolds and piping system filled with glycol.
- Will require maintenance personnel (similar to building hydronic system).
- This system will cost more than an Electric Mat system.
- This system will likely require 3-phase power (less common for residential and is often not allowed by the power company).
- Example: A snowmelt system with a gas fired boiler may require 300,000 BTUs of heat. A comparable electric boiler would require about 250 amps (3-phase 208 volt) to give the same amount of heat.
- Using an electric boiler could potentially increase the building electrical service to the next available size. This has the potential to increase new building impact fees.
- Electric Boiler
- General Considerations:
- Concrete surface – tubing must be at least 2” below the surface of the concrete but must also be less than 6” below the surface of the concrete.
- Sand base/paver – tubing must have 1” (minimum) of sand between the tubing and the paver after the vibrating during installation is complete.
- Asphalt (Blacktop) – tubing is placed in the gravel base below the asphalt. Asphalt is less conductive than concrete and will require higher operating temperatures to perform as intended.
- Insulation below the snowmelt tubing is recommended to reduce operating costs and improve the system response time (warming up the surface to melt the snow).
- The melted snow will need to be properly drained away from the snowmelt area. Melted snow (melt water) will re-freeze when it leaves the snowmelt area if it is not properly drained.
- Design team needs to know if the area historically has wind that causes snowdrifts (often known by the client or others in the area). Snowdrifts require increased capacity in the system.
Conclusion
Clients will be happier with the snowmelt system when the entire design team considers and communicates the design considerations that have been discussed. As an architect, it is important to know the expectations of the client, construction materials being used, the chosen energy source and any other conditions specific to the project location. Let us help you successfully navigate these issues with our expertise in mechanical, electrical and plumbing systems.